Технология ремонта турбин
Турбокомпрессор является одним из наиболее прецизионных агрегатов двигателя внутреннего сгорания. Ремонт турбокомпрессора (газотурбонагнетателя) любого типа требует четкого соблюдения последовательности технологических операций, перечисленных ниже. Полностью технологический процесс ремонта турбин в Воронеже приведен в Технологической инструкции "Ремонт турбокомпрессоров (газотурбонагнетателей)".
***Производиться предварительный осмотр поступающего в ремонт (или на диагностику) турбокомпрессора на наличие внешних механических повреждений и деформаций корпусных деталей и актуатора.
***Турбокомпрессор полностью разбирается для проведения дефектовки. Как правило, дефектовка производится специалистами предприятия в присутствии Заказчика.
***Производится дефектовка деталей и элементов ТК. Осматриваются внутренние полости корпусов на наличие повреждений, сколов, трещин, вмятин и т.д. Осматривается колесо компрессора на наличие внешних механических повреждений и деформаций. Особое внимание обращается на состояние вала с турбинным колесом. При отсутствии внешних видимых механических повреждений и деформаций, вал устанавливается в призмы для проверки радиального биения. После всего вышеперечисленного принимается решение о пригодности дальнейшей эксплуатации колеса компрессора и вала с турбинным колесом.
***Дефектовка радиальных подшипников, упорного подшипника, дистанционных втулок, уплотнительных колец, манжет и прокладок не производится - перечисленные элементы при ремонте заменяются на новые автоматически.
***Все корпусные детали и колеса (если они не подлежат замене) тщательно очищаются в пескоструйной камере. Внутренняя полость корпуса подшипников при очистке изолируется от попадания внутрь песка специальными заглушками. Вал изолируется при очистке специальной оправкой во избежание повреждений поверхностей трения и посадочных поверхностей, производится очистка только лопастей турбинного колеса. У компрессорного колеса при очистке изолируется посадочная поверхность.
***После очистки детали и элементы тщательно обдуваются сжатым воздухом, заглушки и оправки удаляются, корпус подшипников, колесо компрессора и вал с турбинным колесом промываются в специальном составе, после чего повторно обдуваются сжатым воздухом.
***Производится первый этап четырехступенчатого балансировочного цикла. Вал с турбинным колесом балансируется на стенде СМТ-47tr. Частота вращении вала – 2000-4000 об/мин. Это самый важный этап балансировочного цикла, от него в большей мере зависит итог всего балансировочного цикла.
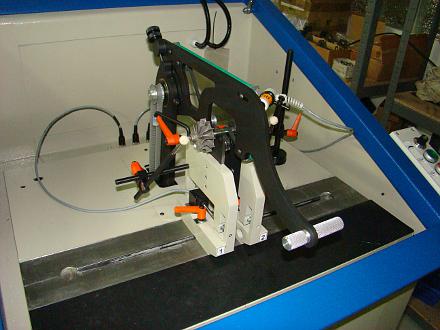
***Второй этап цикла - балансировка ротора в сборе (вал с турбинным колесом-дистанционные втулки-колесо компрессора-гайка) на том же стенде СМТ-47tr, только по другим калибровочным данным. Частота вращении ротора – 2000-4000 об/мин.
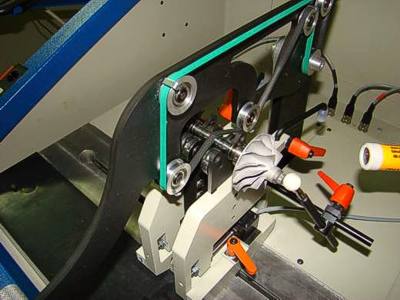
***Производится сборка картриджа турбокомпрессора. Детали и элементы перед сборкой картриджа обдуваются сжатым воздухом, при сборке требуется соблюдать стерильность, используется чистая ветошь и чистое моторное масло. Масляные каналы радиальных подшипников, упорного подшипника, корпуса подшипников повторно проверяются на отсутствие загрязнений и посторонних предметов.
***Картридж устанавливается на стенд СМТ-48TWIN, положение «А». Подключается маслоподающая магистраль. Моторное масло в стенде прогревается до температуры 45-55 градусов. Давление масла - 5 атм. Практически, на этом этапе создаются рабочие условия эксплуатации турбокомпрессора на автомобиле. Производится следующий, третий этап балансировочного цикла. Ротор турбокомпрессора балансируется на этом этапе на частотах 10000-25000 об/мин. в двух плоскостях. Одновременно картридж проверяется визуально на утечку масла с компрессорной и турбинной сторон.
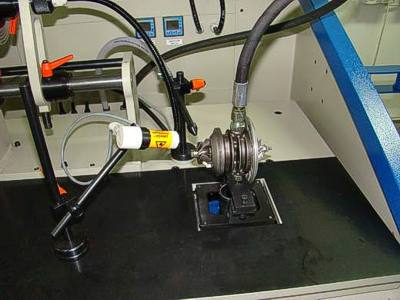
***Завершающий, четвертый этап балансировочного цикла производится на стенде СМТ-48TWIN, положение «Б». Этот этап больше контрольный, чем балансировочный. При проведении квалифицированной балансировки на первых трех этапах, добалансировка на завершающем этапе практически не требуется. Картридж разгоняется с положения покоя до своих максимально допустимых (паспортных) оборотов, при этом во всем диапазоне рабочих частот снимаются значения остаточного дисбаланса и отображаются в виде графика на мониторе. При необходимости, значение остаточного дисбаланса на каком-либо участке рабочего диапазоне корректируется методом удаления массы.
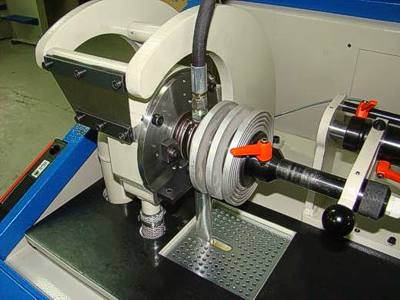
***После завершения балансировочного цикла картридж снимается со стенда, маслоподающий и маслосливной каналы корпуса подшипников блокируются заглушками во избежание попадания пыли и грязи внутрь. Производиться окончательная сборка турбокомпрессора, гайка крепления компрессорного колеса маркируется, окончательные значения остаточного дисбаланса заносятся в Гарантийный талон.